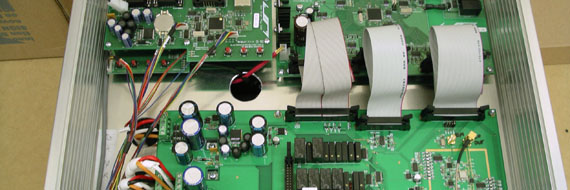
Often the issue of how to test electronic modules is all but forgotten until it is time to set them into mass production – or worse – when equipment starts coming back. In this blog post I want to give you some guide lines on how to tackle end of production line testing.
Where is the End of the Production Line?
This may sound like a silly question with an obvious answer but it isn’t always obvious. If for example an appliance has 2 modules and a motor assembled into a case, is the end of the production line where the complete unit is finished or are there three lines, one for each module and one for the final product.
From the point of view of testing the question comes down to the time and cost added by each sub process, testability at any point and failure rates. If the 2 modules were both built at the same time and had low failure rates and went straight off the end of the line into the appliance then testing at the final appliance stage may be appropriate (assuming effective testing is possible). If however the modules are made overseas and imported for final assembly then the testing had better be before they are shipped from overseas.
Testing at the end of a production line (functional testing) may be handled in a number of ways and they all have their merits.
Technician based test (Specification based)
This test approach takes a skilled person, a list of required tests and access to a stack of generic test equipment. There may be some basic automation of some of the measurement sequences but basically it is a manual test by a skilled person. This type of testing is suitable for total lifetime production quantities of up to a few hundred and batch sizes are of up to about 100 pieces. The nature of the product does not impact the quantity decision point much. If it is a very complex test then it will be more expensive to test this way – but so will the alternate approaches. The quality of the testing is strongly dependent on the skill of the tester.
Operator Based Test (Procedure Based)
This test approach involves a non technical operator, a very clear test procedure and some generic test equipment (but models specified in the test procedure) and maybe some special firmware in the product and some test jigs. This type of testing it suitable for lifetime production quantities from a few hundred to about 10,000 to 20,000 units. The upper limit on the suitability of this type of testing can be much lower if the cost of failure of the product is high (safety or very high field replacement cost). The quality of the testing is somewhat dependent on the attention and attitude of the operator and the skill of the person who set up the test.
Automated Functional Testing
Automated Functional Testing requires a collection of test gear integrated together into a tester or a fully integrated automated functional tester. The part is loaded in (often the only operator assisted part of the test) and fully tested. This type of testing is suitable where lifetime quantities are over 10,000 to 20,000 or less if there is a high cost associated with failure. The quality of the testing is nearly entirely down to the skill of the designers of the test system and the operator has little influence on test results.
Summary
When embarking on an electronic module design and manufacture project it pays to ask “How will this be tested?” and “At what point will this be tested?” early in the project. Different approaches are suitable mostly according to the volume rather than the complexity.
Leave a Reply